Pick Modules
- Jerry Schultz, P.E.
- Sep 4, 2020
- 4 min read
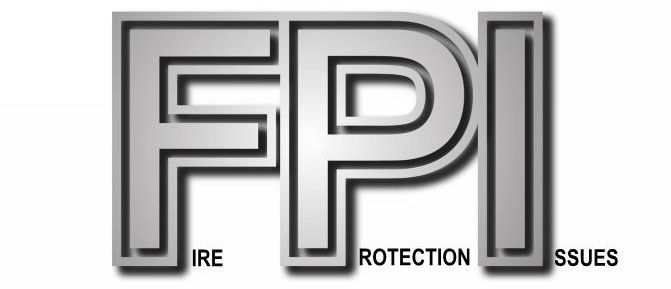
Walmart, Amazon, Lowes, Target and numerous third party logistic (3PL) firms are shifting to pick modules as their warehouse arrangement. A pick module consists of an arrangement of racking with catwalk levels supported from the racking supports on about 10 foot vertical increments so that employees (or robots) can pick the product from a shelf and transport it to the shipping area.

Photo 1: Pick Module Top Level
In the photo above, the “floor” (more properly designated as a catwalk level) of the pick module is supported from the racking shown and the rack system is designed to support the catwalk levels. The photo shows the top level of the racking system, and there can be multiple levels below. This allows for an employee to walk the level and select product from the shelf to transport to the packaging and shipping areas. Most of these installations have conveyors running on the levels so that the product is moved to the packaging and shipping area by itself.
Having provided fire protection engineering and code consulting for numerous pick modules, FPI provides the following for those individuals that are dealing with their first pick module. We believe there are several issues that need to be addressed and understood by all.
Occupant load is higher than normally anticipated in a storage occupancy. This will require a careful evaluation of the design strategies for fire alarm, exiting and fire fighter access.
The catwalk levels are not to be classified as a story so they do not impact the height and area limitations.
Nor do they fall into a floor classification. They do not provide a true separation in that the walking surface is typically a product called Resindek and provides no fire resistance. The module itself is open to the warehouse on the sides.
There is typically a lift provided to move products from the ground level to the appropriate upper level. This lift is not an elevator but instead is a vertical reciprocating conveyor. No recall functions are provided and employees are not supposed to be on the lift.
Exiting from upper levels is via stairs. The rack designer initially tries to only provide these open stairs within the pick module and take into account vertical travel distance down the stairs to the outside. On all levels, it is important to be aware of any conveyors as traveling around a conveyor will add travel distance. If an exit cannot be reached within the allowable travel distance (which may be as small as 250 feet depending upon the year and interpretation of the code), interior fire rated stair enclosures will be needed.
Sprinklers are required on every level. The sprinkler system must be designed to current code, which may include barriers within the shelving units.
The shelves will be provided with open face boxes to allow for “picking” the product. If plastic boxes are provided for durability reasons, the sprinkler system design must take this higher hazard material into account.
Each client that we have worked with has their own set of fire protection requirements. At the current time, there is no one set of answers.
The local official has to be part of the design efforts starting with an initial kick off meeting where the concept of a pick module is explained and fire protection features are discussed. Even though the community is happy to get one of these buildings in their area and it typically provides a nice tax base, the code official has to worry about the fire protection and the life safety of the employees. The input from the official on the front end eliminates the need for critical revisions when the building is trying to get its Certificate of Occupancy. FPI identifies this as “No surprises” and we consider this a fundamental role of the consultant.
The fire alarm system and building management system must be carefully coordinated. This is not a typical warehouse occupancy with a limited occupant load, no air conditioning, no or limited conveyors throughout the building, and occupants at grade level, therefore additional life safety considerations must be incorporated into the design. Notification appliances should be provided. The fire alarm system may need to tie into an HVAC system and shut the system down. Conveyors should probably be shut down. Travel distances have to take into vertical distances down the stairs.
As fire protection engineers that have worked on numerous pick modules, The Fire Protection International Consortium, Inc. believes that this sector of the marketplace requires the full involvement of a Fire Protection Engineer as a consultant throughout the entire project. It is the involvement of the fire protection consultant that can ensure that all life safety systems are addressed early on in the project. This will ensure that all design issues are addressed and reviewed by all stakeholders. It will also serve to reduce change orders as a result of plan review comments or surprises at the end of the project when trying to get the Certificate of Occupancy.
It wasn’t one of our projects, but we are aware of a code official requiring additional stairs before he would issue the Certificate of Occupancy because he felt that more were needed. This resulted in a delay in the go live date along with a loss of storage capacity.
Pick module projects require a Fire Protection Engineer to ensure NO SURPRISES!
As always, I welcome your comments: j.schultz@the-fpi.com
コメント